Automatic Change-based Diagnosis of Structures Using Spatiotemporal Data and As- Designed Model
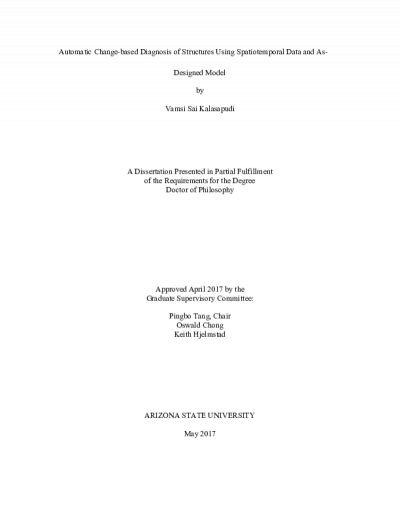
Description
Civil infrastructures undergo frequent spatial changes such as deviations between as-designed model and as-is condition, rigid body motions of the structure, and deformations of individual elements of the structure, etc. These spatial changes can occur during the design phase, the construction phase, or during the service life of a structure. Inability to accurately detect and analyze the impact of such changes may miss opportunities for early detections of pending structural integrity and stability issues. Commercial Building Information Modeling (BIM) tools could hardly track differences between as-designed and as-built conditions as they mainly focus on design changes and rely on project managers to manually update and analyze the impact of field changes on the project performance. Structural engineers collect detailed onsite data of a civil infrastructure to perform manual updates of the model for structural analysis, but such approach tends to become tedious and complicated while handling large civil infrastructures.
Previous studies started collecting detailed geometric data generated by 3D laser scanners for defect detection and geometric change analysis of structures. However, previous studies have not yet systematically examined methods for exploring the correlation between the detected geometric changes and their relation to the behaviors of the structural system. Manually checking every possible loading combination leading to the observed geometric change is tedious and sometimes error-prone. The work presented in this dissertation develops a spatial change analysis framework that utilizes spatiotemporal data collected using 3D laser scanning technology and the as-designed models of the structures to automatically detect, classify, and correlate the spatial changes of a structure. The change detection part of the developed framework is computationally efficient and can automatically detect spatial changes between as-designed model and as-built data or between two sets of as-built data collected using 3D laser scanning technology. Then a spatial change classification algorithm automatically classifies the detected spatial changes as global (rigid body motion) and local deformations (tension, compression). Finally, a change correlation technique utilizes a qualitative shape-based reasoning approach for identifying correlated deformations of structure elements connected at joints that contradicts the joint equilibrium. Those contradicting deformations can help to eliminate improbable loading combinations therefore guiding the loading path analysis of the structure.
Previous studies started collecting detailed geometric data generated by 3D laser scanners for defect detection and geometric change analysis of structures. However, previous studies have not yet systematically examined methods for exploring the correlation between the detected geometric changes and their relation to the behaviors of the structural system. Manually checking every possible loading combination leading to the observed geometric change is tedious and sometimes error-prone. The work presented in this dissertation develops a spatial change analysis framework that utilizes spatiotemporal data collected using 3D laser scanning technology and the as-designed models of the structures to automatically detect, classify, and correlate the spatial changes of a structure. The change detection part of the developed framework is computationally efficient and can automatically detect spatial changes between as-designed model and as-built data or between two sets of as-built data collected using 3D laser scanning technology. Then a spatial change classification algorithm automatically classifies the detected spatial changes as global (rigid body motion) and local deformations (tension, compression). Finally, a change correlation technique utilizes a qualitative shape-based reasoning approach for identifying correlated deformations of structure elements connected at joints that contradicts the joint equilibrium. Those contradicting deformations can help to eliminate improbable loading combinations therefore guiding the loading path analysis of the structure.
Date Created
The date the item was original created (prior to any relationship with the ASU Digital Repositories.)
2017
Agent
- Author (aut): Kalasapudi, Vamsi Sai
- Thesis advisor (ths): Tang, Pingbo
- Committee member: Chong, Oswald
- Committee member: Hjelmstad, Keith
- Publisher (pbl): Arizona State University