Multiphase Direct Ink Writing: Nature-Inspired Layer Patterning For Structural and Functional Versatility
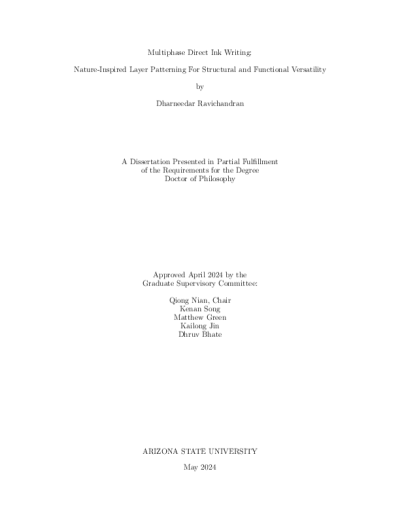
Description
Additive manufacturing, also known as 3D printing, has revolutionized modern manufacturing in several key areas: complex geometry fabrication, rapid prototyping and iteration, customization and personalization, reduced material waste, supply chain flexibility, complex assemblies and consolidated parts, and material innovation. As the technology continues to evolve, its impact on manufacturing is expected to grow, driving further innovation and reshaping traditional production processes. Some innovation examples in this field are inspired by natural or bio-systems, such as honeycomb structures for internal morphological control to increase strength, bio-mimetic composites for scaffold structures, or shape memory materials in 4D printing for targeted drug delivery. However, the technology is limited by its ability to manipulate multiple materials, especially tuning their submicron characteristics when they show non-compatible chemical or physical features. For example, the deposition and patterning of nanoparticles with different dimensions have seen little success, except in highly precise and slow 3D printing processes like aerojet or electrohydrodynamic. Taking inspiration from the layered patterns and structures found in nature, this research aims to demonstrate the development and versatility of a newly developed ink-based composite 3D printing mechanism called multiphase direct ink writing (MDIW). The MDIW is a multi-materials extrusion system, with a unique nozzle design that can accommodate two immiscible and non-compatible polymer or nano-composite solutions as feedstock. The intricate internal structure of the nozzle enables the rearrangement of the feedstock in alternating layers (i.e., ABAB...) and multiplied within each printed line. This research will first highlight the design and development of the MDIW 3D printing mechanism, followed by laminate processing to establish the requirements of layer formation in the XY-axis and the effect of layer formation on its microstructural and mechanical properties. Next, the versatility of the mechanism is also shown through the one-step fabrication of shape memory polymers with dual stimuli responsiveness, highlighting the 4D printing capabilities. Moreover, the MDIW's capability of dual nanoparticle patterning for manufacturing multi-functional carbon-carbon composites will be highlighted. Comprehensive and in-depth studies are conducted to investigate the morphology-structure-property relationships, demonstrating potential applications in structural engineering, smart and intelligent devices, miniature robotics, and high-temperature systems.
Date Created
The date the item was original created (prior to any relationship with the ASU Digital Repositories.)
2024
Agent
- Author (aut): Ravichandran, Dharneedar
- Thesis advisor (ths): Nian, Qiong
- Committee member: Song, Kenan
- Committee member: Green, Matthew
- Committee member: Jin, Kailong
- Committee member: Bhate, Dhruv
- Publisher (pbl): Arizona State University