Leveraging Teamwork and Unskilled Labor in Facilities Zone Maintenance
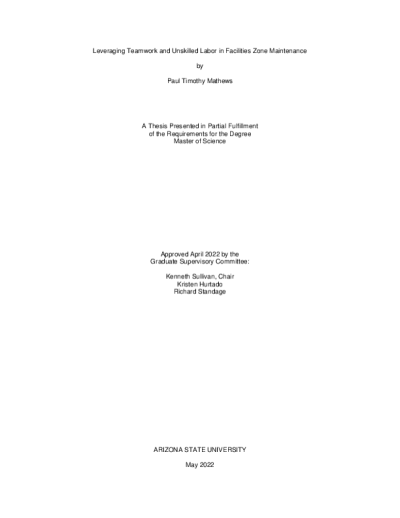
Description
Facilities Management is a service that should follow economic concepts of “value added” and “cost-effectiveness.” Facilities sites and campuses can be divided into geographic facilities maintenance zones to improve response time, coordination of trades, customer service, and the ownership or accountability of technicians. Facilities zone maintenance teams of multi-trade technicians can work together in a dynamic partnership to significantly reduce costs and do more with less. Six months of field research, case studies, and crew balance analysis of primary quantitative data was used to deductively evaluate the effectiveness of the zone maintenance model. To fill gaps in skilled labor, reduce maintenance costs, and increase available skilled labor capacity the maintenance zone implemented a strategy to better utilize and schedule the labor of unskilled entry level maintenance technicians. A teamwork approach was also used to share the collective multi-trade workload and allow the zone maintenance crew to accomplish more than individual technicians could do alone.
A comprehensive literature review revealed an alarming lack of facilities management research and the vast disconnect between academic assumptions and practical real-world applications. It is evident from the case studies that more effective utilization of unskilled labor and harnessing the unique capacity of a multi-trade team are important competitive advantages of the facilities zone maintenance model. These intangible contributions and the value added to the organization can be measured and quantified through careful data collection and analysis. These studies are a reminder that significant maintenance cost savings can be achieved by eliminating labor waste and crew scheduling inefficiencies. Value can be added to the organization by reducing these and other intangible costs by focusing on continuous improvement, productivity, efficiency, and effective workflow.
Date Created
The date the item was original created (prior to any relationship with the ASU Digital Repositories.)
2022
Agent
- Author (aut): Mathews, Paul
- Thesis advisor (ths): Sullivan, Kenneth
- Committee member: Hurtado, Kristen
- Committee member: Standage, Richard
- Publisher (pbl): Arizona State University