Deformation and Damage in Fiber Reinforced Polymer and Ceramic Matrix Composite Materials
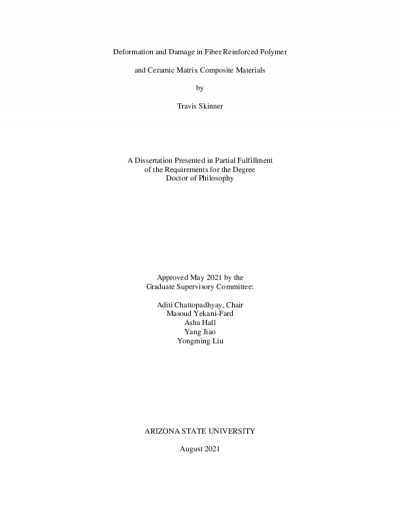
Description
Fiber reinforced composites are rapidly replacing conventional metallic or polymeric materials as materials of choice in a myriad of applications across a wide range of industries. The relatively low weight, high strength, high stiffness, and a variety of thermal and mechanical environmental and loading capabilities are in part what make composite materials so appealing to material experts and design engineers. Additionally, fiber reinforced composites are highly tailorable and customized composite materials and structures can be readily designed for specific applications including those requiring particular directional material properties, fatigue resistance, damage tolerance, high temperature capabilities, or resistance to environmental degradation due to humidity and oxidation. The desirable properties of fiber reinforced composites arise from the strategic combination of multiple constituents to form a new composite material. However, the significant material anisotropy that occurs as a result of combining multiple constituents, each with different directional thermal and mechanical properties, complicates material analysis and remains a major impediment to fully understanding composite deformation and damage behavior. As a result, composite materials, especially specialized composites such as ceramic matrix composites and various multifunctional composites, are not utilized to their fullest potential. In the research presented in this dissertation, the deformation and damage behavior of several fiber reinforced composite systems were investigated. The damage accumulation and propagation behavior of carbon fiber reinforced polymer (CFRP) composites under complex in-phase biaxial fatigue loading conditions was investigated and the early stage damage and microscale damage were correlated to the eventual fatigue failure behavior and macroscale damage mechanisms. The temperature-dependent deformation and damage response of woven ceramic matrix composites (CMCs) reinforced with carbon and silicon carbide fibers was also studied. A fracture mechanics-informed continuum damage model was developed to capture the brittle damage behavior of the ceramic matrix. A multiscale thermomechanical simulation framework, consisting of cooldown simulations to capture a realistic material initial state and subsequent mechanical loading simulations to capture the temperature-dependent nonlinear stress-strain behavior, was also developed. The methodologies and results presented in this research represent substantial progress toward increasing understanding of the deformation and damage behavior of some key fiber reinforced composite materials.
Date Created
The date the item was original created (prior to any relationship with the ASU Digital Repositories.)
2021
Agent
- Author (aut): Skinner, Travis Dale
- Thesis advisor (ths): Chattopadhyay, Aditi
- Committee member: Hall, Asha
- Committee member: Liu, Yongming
- Committee member: Jiao, Yang
- Committee member: Yekani-Fard, Masoud
- Publisher (pbl): Arizona State University