A Current-Mode, Dynamic Hysteresis Hybrid Supply Modulator for Wideband LTE Applications
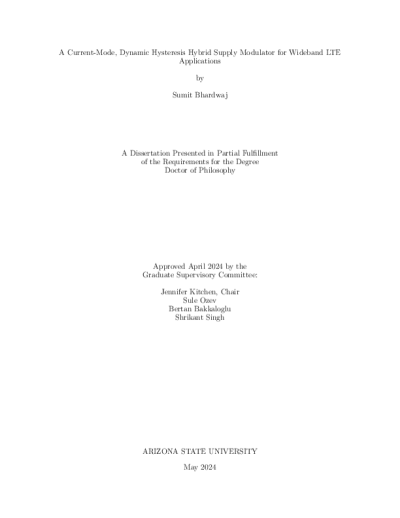
Description
The world has seen a revolution in cellular communication with the advent of 5G (fifth-generation), which enables gigabits per second data speed with low latency, massive capacity, and increased availability. These modern wireless systems improve spectrum efficiency by employing advanced modulation techniques, but result in large peak-to-average power ratios (PAPR) of the transmitted signals that degrades the efficiency of the radio-frequency power amplifiers (PAs) in the power back-off (PBO) region. Envelope tracking (ET), which is a dynamic supply control technology to realize high efficiency PAs, is a promising approach for designing transmitters for the future. Conventional voltage regulators, such as linear regulators and switching regulators, fail to simultaneously offer high speed, high efficiency, and improved linearity. Hybrid supply modulators (HSM) that combine a linear and switching regulator emerge as promising solutions to achieve an optimized tradeoff between different design parameters. Over the years, considerable development and research efforts in industry and academia have been spent on maximizing HSM performance, and a majority of the most recently developed modulators are implemented in CMOS technology and mainly targeted for handset applications. In this dissertation, the main requirements for modern HSM designs are categorized and analyzed in detail. Next, techniques to improve HSM performance are discussed. The available device technologies for HSM and PA implementations are also delineated, and implementation challenges of an integrated ET-PA system are summarized. Finally, a Current-Mode with Dynamic Hysteresis HSM is proposed, designed, and implemented. With the proposed technique, the HSM is able to track LTE signals up to 100 MHz bandwidth. Switching at a peak frequency of 40 MHz, the design is able to track a 1 Vpp sinusoidal signal with high fidelity, has an output voltage ripple around 54 mV, and achieves a peak static and dynamic efficiency of 92.2% and 82.29%, respectively, at the maximum output. The HSM is capable of delivering a maximum output power of 425 mW and occupies a small die area of 1.6mm2. Overall, the proposed HSM promises competitive performance compared to state-of-the-art works.
Date Created
The date the item was original created (prior to any relationship with the ASU Digital Repositories.)
2024
Agent
- Author (aut): BHARDWAJ, SUMIT
- Thesis advisor (ths): Kitchen, Jennifer
- Committee member: Ozev, Sule
- Committee member: Bakkaloglu, Bertan
- Committee member: Singh, Shrikant
- Publisher (pbl): Arizona State University