Optimized Anode, Cathode, Coolant Flow Designs and Optimization of Operating Conditions for Enhanced Performance of Proton Exchange Membrane Fuel Cells
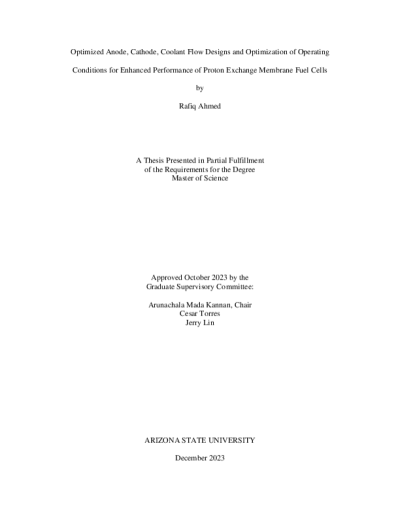
Description
This study deals with various flow field designs for anode, cathode, and coolant plates for optimizing the performance of proton exchange membrane fuel cell using H2 and air. In particular, the 3D models with various flow field patterns such as single parallel serpentine (anode), multi parallel (anode), multi-parallel serpentine (cathode), multi serpentine (cathode) have been evaluated for enhancing the fuel cell performance at 60 oC, with three different coolant flow designs (mirror serpentine, multi serpentine and parallel serpentine). Both the peak power and limiting current density are considered based on the parameters such as temperature distribution, pressure distribution, reactants/species distribution and the membrane water content on the active area (50 cm2) region. It is interesting to note that the coolant channel also has a significant effect in regulating the fuel cell performance at high current densities, in addition to reactant gas flow channels. The simulated single cell with Nafion (thickness: 18 m) demonstrates a peak power density of 0.97 W.cm-2 with single parallel serpentine (anode), multi parallel serpentine (cathode) and serpentine (coolant) and 0.91 W.cm-2 with multi parallel (anode), multi serpentine (cathode), and parallel serpentine (coolant) flow field designs. The simulated fuel cell performance is also experimentally validated with four cells at 60 oC using H2 fuel and air as the oxidant.
Date Created
The date the item was original created (prior to any relationship with the ASU Digital Repositories.)
2023
Agent
- Author (aut): Ahmed, Rafiq
- Thesis advisor (ths): Mada Kannan, Arunachala
- Committee member: Torres, Cesar
- Committee member: Lin, Jerry
- Publisher (pbl): Arizona State University