Multiscale Modeling of Polymer and Ceramic Matrix Composites
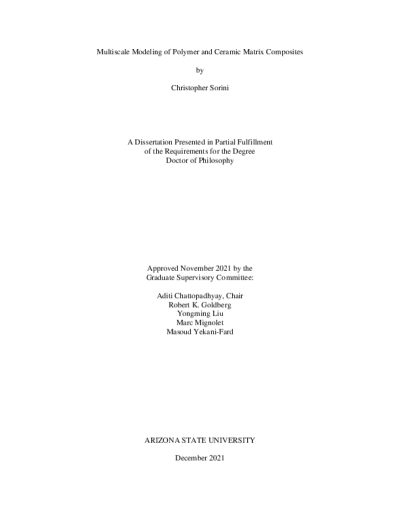
Description
Advanced Polymer and Ceramic Matrix Composites (PMCs and CMCs) are currently employed in a variety of airframe and engine applications. This includes PMC jet engine fan cases and CMC hot gas path turbine components. In an impact event, such as a jet engine fan blade-out, PMCs exhibit significant deformation-induced temperature rises in addition to strain rate, temperature, and pressure dependence. CMC turbine components experience elevated temperatures, large thermal gradients, and sustained loading for long time periods in service, where creep is a major issue. However, the complex nature of woven and braided composites presents significant challenges for deformation, progressive damage, and failure prediction, particularly under extreme service conditions where global response is heavily driven by competing time and temperature dependent phenomena at the constituent level. In service, the constituents in these advanced composites experience history-dependent inelastic deformation, progressive damage, and failure, which drive global nonlinear constitutive behavior. In the case of PMCs, deformation-induced heating under impact conditions is heavily influenced by the matrix. The creep behavior of CMCs is a complex manifestation of time-dependent load transfer due to the differing creep rates of the constituents; simultaneous creep and relaxation at the constituent level govern macroscopic CMC creep. The disparity in length scales associated with the constituent materials, woven and braided tow architectures, and composite structural components therefore necessitates the development of robust multiscale computational tools. In this work, multiscale computational tools are developed to gain insight into the deformation, progressive damage, and failure of advanced PMCs and CMCs. This includes multiscale modeling of the impact response of PMCs, including adiabatic heating due to the conversion of plastic work to heat at the constituent level, as well as elevated temperature creep in CMCs as a result of time-dependent constituent load transfer. It is expected that the developed models and methods will provide valuable insight into the challenges associated with the design and certification of these advanced material systems.
Date Created
The date the item was original created (prior to any relationship with the ASU Digital Repositories.)
2021
Agent
- Author (aut): Sorini, Christopher
- Thesis advisor (ths): Chattopadhyay, Adit
- Committee member: Goldberg, Robert K
- Committee member: Liu, Yongming
- Committee member: Mignolet, Marc
- Committee member: Yekani-Fard, Masoud
- Publisher (pbl): Arizona State University