Quantification of solar photovoltaic encapsulant browning level using image processing tool
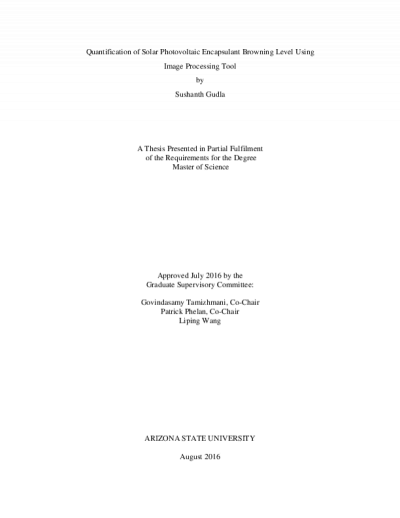
Description
In recent years, solar photovoltaic (PV) industry has seen lots of improvements in technology and of growth in market with crystalline silicon PV modules being the most widely used technology. Plant inspections are gaining much importance to identify and quantitatively determine the impacts of various visual defects on performance. There are about 86 different types of defects found in the PV modules installed in various climates and most of them can be visually observed. However, a quantitative determination of impact or risk of each of identified defect on performance is challenging. Thus, it is utmost important to quantify the risk for each of the visual defects without any human subjectivity. The best way to quantify the risk of each defect is to perform current-voltage measurements of the defective modules installed in the plant but it requires disruption of plant operation, expensive measuring equipment and intensive human resources. One of the most riskiest and dominant visual defects is encapsulant browning which affects the PV module performance in the form of current degradation. The present study deals with developing an automated image processing tool which can address the issues of human subjectivity on browning level impacting performance. The image processing tool developed in this work can be directly used to quantify the impact of browning on performance without intrusively disconnecting the modules from the plant. In this work, the quantified browning level impact on performance has also been experimentally validated through a correlation study using short-circuit current and reflectance/transmittance measurements of browned PV modules retrieved from aged plants/systems installed in diverse climatic conditions. The primary goal of the image processing tool developed in this work is to determine the performance impact of encapsulant browning without interrupting the plant operation for I-V measurements. The use of image processing tool provides a single numerical value, called browning index (BI), which can accurately quantify browning levels on modules and also correlate with the performance and reflectance/transmittance parameters of the modules.
Date Created
The date the item was original created (prior to any relationship with the ASU Digital Repositories.)
2016
Agent
- Author (aut): Gudla, Sushanth
- Thesis advisor (ths): Govindasamy, Tamizhmani
- Thesis advisor (ths): Patrick, Phelan E
- Committee member: Wang, Liping
- Publisher (pbl): Arizona State University