Efficient extended finite element algorithms for strongly and weakly discontinuous entities with complex internal geometries
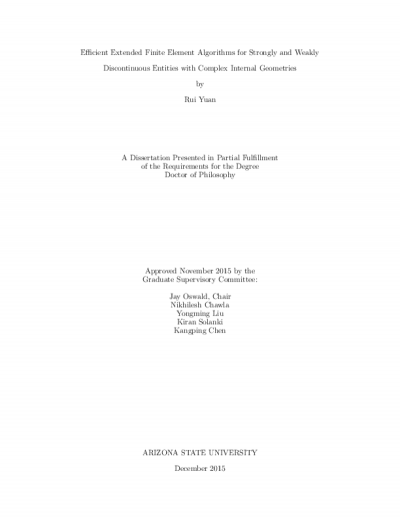
Description
The objective of this research is to develop robust, accurate, and adaptive algorithms in the framework of the extended finite element method (XFEM) for fracture analysis of highly heterogeneous materials with complex internal geometries. A key contribution of this work is the creation of novel methods designed to automate the incorporation of high-resolution data, e.g. from X-ray tomography, that can be used to better interpret the enormous volume of data generated in modern in-situ experimental testing. Thus new algorithms were developed for automating analysis of complex microstructures characterized by segmented tomographic images.
A centrality-based geometry segmentation algorithm was developed to accurately identify discrete inclusions and particles in composite materials where limitations in imaging resolution leads to spurious connections between particles in close contact.To allow for this algorithm to successfully segment geometry independently of particle size and shape, a relative centrality metric was defined to allow for a threshold centrality criterion for removal of voxels that spuriously connect distinct geometries.
To automate incorporation of microstructural information from high-resolution images, two methods were developed that initialize signed distance fields on adaptively-refined finite element meshes. The first method utilizes a level set evolution equation that is directly solved on the finite element mesh through Galerkins method. The evolution equation is formulated to produce a signed distance field that matches geometry defined by a set of voxels segmented from tomographic images. The method achieves optimal convergence for the order of elements used. In a second approach, the fast marching method is employed to initialize a distance field on a uniform grid which is then projected by least squares onto a finite element mesh. This latter approach is shown to be superior in speed and accuracy.
Lastly, extended finite element method simulations are performed for the analysis of particle fracture in metal matrix composites with realistic particle geometries initialized from X-ray tomographic data. In the simulations, particles fracture probabilistically through a Weibull strength distribution. The model is verified through comparisons with the experimentally-measured stress-strain response of the material as well as analysis of the fracture. Further, simulations are then performed to analyze the effect of mesh sensitivity, the effect of fracture of particles on their neighbors, and the role of a particles shape on its fracture probability.
A centrality-based geometry segmentation algorithm was developed to accurately identify discrete inclusions and particles in composite materials where limitations in imaging resolution leads to spurious connections between particles in close contact.To allow for this algorithm to successfully segment geometry independently of particle size and shape, a relative centrality metric was defined to allow for a threshold centrality criterion for removal of voxels that spuriously connect distinct geometries.
To automate incorporation of microstructural information from high-resolution images, two methods were developed that initialize signed distance fields on adaptively-refined finite element meshes. The first method utilizes a level set evolution equation that is directly solved on the finite element mesh through Galerkins method. The evolution equation is formulated to produce a signed distance field that matches geometry defined by a set of voxels segmented from tomographic images. The method achieves optimal convergence for the order of elements used. In a second approach, the fast marching method is employed to initialize a distance field on a uniform grid which is then projected by least squares onto a finite element mesh. This latter approach is shown to be superior in speed and accuracy.
Lastly, extended finite element method simulations are performed for the analysis of particle fracture in metal matrix composites with realistic particle geometries initialized from X-ray tomographic data. In the simulations, particles fracture probabilistically through a Weibull strength distribution. The model is verified through comparisons with the experimentally-measured stress-strain response of the material as well as analysis of the fracture. Further, simulations are then performed to analyze the effect of mesh sensitivity, the effect of fracture of particles on their neighbors, and the role of a particles shape on its fracture probability.
Date Created
The date the item was original created (prior to any relationship with the ASU Digital Repositories.)
2015
Agent
- Author (aut): Yuan, Rui
- Thesis advisor (ths): Oswald, Jay
- Committee member: Chawla, Nikhilesh
- Committee member: Liu, Yongming
- Committee member: Solanki, Kiran
- Committee member: Chen, Kangping
- Publisher (pbl): Arizona State University