Automation of risk priority number calculation of photovoltaic modules and evaluation of module level power electronics
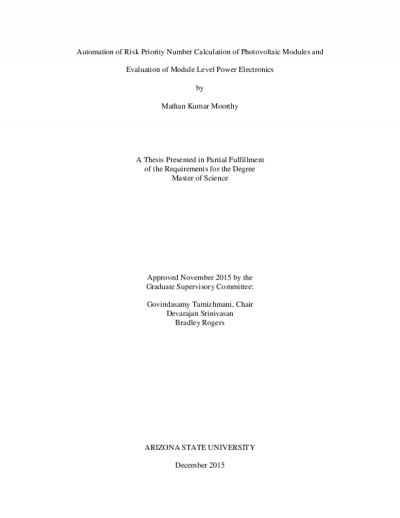
Description
This is a two part thesis:
Part – I
This part of the thesis involves automation of statistical risk analysis of photovoltaic (PV) power plants. Statistical risk analysis on the field observed defects/failures in the PV power plants is usually carried out using a combination of several manual methods which are often laborious, time consuming and prone to human errors. In order to mitigate these issues, an automated statistical risk analysis (FMECA) is necessary. The automation developed and presented in this project generates about 20 different reliability risk plots in about 3-4 minutes without the need of several manual labor hours traditionally spent for these analyses. The primary focus of this project is to automatically generate Risk Priority Number (RPN) for each defect/failure based on two Excel spreadsheets: Defect spreadsheet; Degradation rate spreadsheet. Automation involves two major programs – one to calculate Global RPN (Sum of Performance RPN and Safety RPN) and the other to find the correlation of defects with I-V parameters’ degradations. Based on the generated RPN and other reliability plots, warranty claims for material defect and degradation rate may be made by the system owners.
Part – II
This part of the thesis involves the evaluation of Module Level Power Electronics (MLPE) which are commercially available and used by the industry. Reliability evaluations of any product typically involve pre-characterizations, many different accelerated stress tests and post-characterizations. Due to time constraints, this part of the project was limited to only pre-characterizations of about 100 MLPE units commercially available from 5 different manufacturers. Pre-characterizations involve testing MLPE units for rated efficiency, CEC efficiency, power factor and Harmonics (Vthd (%) and Ithd (%)). The pre-characterization test results can be used to validate manufacturer claims and to evaluate the product for compliance certification test standards. Pre-characterization results were compared for all MLPE units individually for all tested parameters listed above. The accelerated stress tests are ongoing and are not presented in this thesis. Based on the pre-characterizations presented in this report and post-characterizations performed after the stress tests, the pass/fail and time-to-failure analyses can be carried out by future researchers.
Part – I
This part of the thesis involves automation of statistical risk analysis of photovoltaic (PV) power plants. Statistical risk analysis on the field observed defects/failures in the PV power plants is usually carried out using a combination of several manual methods which are often laborious, time consuming and prone to human errors. In order to mitigate these issues, an automated statistical risk analysis (FMECA) is necessary. The automation developed and presented in this project generates about 20 different reliability risk plots in about 3-4 minutes without the need of several manual labor hours traditionally spent for these analyses. The primary focus of this project is to automatically generate Risk Priority Number (RPN) for each defect/failure based on two Excel spreadsheets: Defect spreadsheet; Degradation rate spreadsheet. Automation involves two major programs – one to calculate Global RPN (Sum of Performance RPN and Safety RPN) and the other to find the correlation of defects with I-V parameters’ degradations. Based on the generated RPN and other reliability plots, warranty claims for material defect and degradation rate may be made by the system owners.
Part – II
This part of the thesis involves the evaluation of Module Level Power Electronics (MLPE) which are commercially available and used by the industry. Reliability evaluations of any product typically involve pre-characterizations, many different accelerated stress tests and post-characterizations. Due to time constraints, this part of the project was limited to only pre-characterizations of about 100 MLPE units commercially available from 5 different manufacturers. Pre-characterizations involve testing MLPE units for rated efficiency, CEC efficiency, power factor and Harmonics (Vthd (%) and Ithd (%)). The pre-characterization test results can be used to validate manufacturer claims and to evaluate the product for compliance certification test standards. Pre-characterization results were compared for all MLPE units individually for all tested parameters listed above. The accelerated stress tests are ongoing and are not presented in this thesis. Based on the pre-characterizations presented in this report and post-characterizations performed after the stress tests, the pass/fail and time-to-failure analyses can be carried out by future researchers.
Date Created
The date the item was original created (prior to any relationship with the ASU Digital Repositories.)
2015
Agent
- Author (aut): Moorthy, Mathan Kumar
- Thesis advisor (ths): Govindasamy, Tamizhmani
- Committee member: Devarajan, Srinivasan
- Committee member: Bradley, Rogers
- Publisher (pbl): Arizona State University