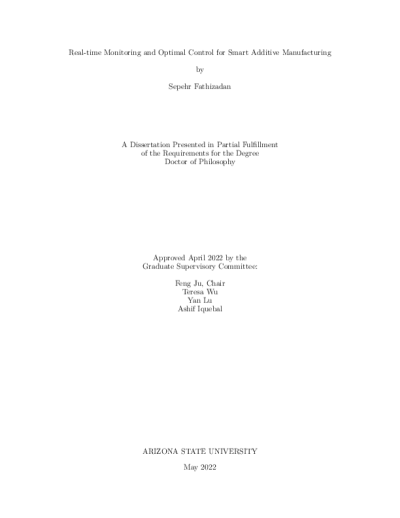
Description
Additive manufacturing consists of successive fabrication of materials layer upon layer to manufacture three-dimensional items. Several key problems such as poor quality of finished products and excessive operational costs are yet to be addressed before it becomes widely applicable in the industry. Retroactive/offline actions such as post-manufacturing inspections for defect detection in finished products are not only extremely expensive and ineffective but are also incapable of issuing corrective action signals during the building span. In-situ monitoring and optimal control methods, on the other hand, can provide viable alternatives to aid with the online detection of anomalies and control the process. Nevertheless, the complexity of process assumptions, unique structure of collected data, and high-frequency data acquisition rate severely deteriorates the performance of traditional and parametric control and process monitoring approaches. Out of diverse categories of additive manufacturing, Large-Scale Additive Manufacturing (LSAM) by material extrusion and Laser Powder Bed Fusion (LPBF) suffer the most due to their more advanced technologies and are therefore the subjects of study in this work. In LSAM, the geometry of large parts can impact the heat dissipation and lead to large thermal gradients between distance locations on the surface. The surface's temperature profile is captured by an infrared thermal camera and translated to a non-linear regression model to formulate the surface cooling dynamics. The surface temperature prediction methodology is then combined into an optimization model with probabilistic constraints for real-time layer time and material flow control. On-axis optical high-speed cameras can capture streams of melt pool images of laser-powder interaction in real-time during the process. Model-agnostic deep learning methods offer a great deal of flexibility when facing such unstructured big data and thus are appealing alternatives to their physical-related and regression-based modeling counterparts. A configuration of Convolutional Long-Short Term Memory (ConvLSTM) auto-encoder is proposed to learn a deep spatio-temporal representation from sequences of melt pool images collected from experimental builds. The unfolded bottleneck tensors are then further mined to construct a high accuracy and low false alarm rate anomaly detection and monitoring procedure.
Details
Title
- Real-time Monitoring and Optimal Control for Smart Additive Manufacturing
Contributors
- Fathizadan, Sepehr (Author)
- Ju, Feng (Thesis advisor)
- Wu, Teresa (Committee member)
- Lu, Yan (Committee member)
- Iquebal, Ashif (Committee member)
- Arizona State University (Publisher)
Date Created
The date the item was original created (prior to any relationship with the ASU Digital Repositories.)
2022
Subjects
Resource Type
Collections this item is in
Note
- Partial requirement for: Ph.D., Arizona State University, 2022
- Field of study: Industrial Engineering