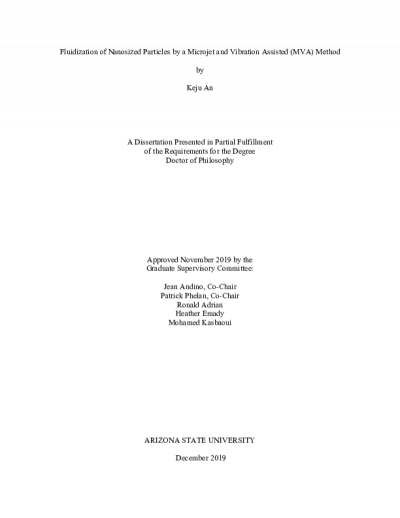
Description
The applications utilizing nanoparticles have grown in both industrial and academic areas because of the very large surface area to volume ratios of these particles. One of the best ways to process and control these nanoparticles is fluidization. In this work, a new microjet and vibration assisted (MVA) fluidized bed system was developed in order to fluidize nanoparticles. The system was tested and the parameters optimized using two commercially available TiO2 nanoparticles: P25 and P90. The fluidization quality was assessed by determining the non-dimensional bed height as well as the non-dimensional pressure drop. The non-dimensional bed height for the nanosized TiO2 in the MVA system optimized at about 5 and 7 for P25 and P90 TiO2, respectively, at a resonance frequency of 50 Hz. The non-dimensional pressure drop was also determined and showed that the MVA system exhibited a lower minimum fluidization velocity for both of the TiO2 types as compared to fluidization that employed only vibration assistance. Additional experiments were performed with the MVA to characterize the synergistic effects of vibrational intensity and gas velocity on the TiO2 P25 and P90 fluidized bed heights. Mathematical relationships were developed to correlate vibrational intensity, gas velocity, and fluidized bed height in the MVA. The non-dimensional bed height in the MVA system is comparable to previously published P25 TiO2 fluidization work that employed an alcohol in order to minimize the electrostatic attractions within the bed. However, the MVA system achieved similar results without the addition of a chemical, thereby expanding the potential chemical reaction engineering and environmental remediation opportunities for fluidized nanoparticle systems.
In order to aid future scaling up of the MVA process, the agglomerate size distribution in the MVA system was predicted by utilizing a force balance model coupled with a two-fluid model (TFM) simulation. The particle agglomerate size that was predicted using the computer simulation was validated with experimental data and found to be in good agreement.
Lastly, in order to demonstrate the utility of the MVA system in an air revitalization application, the capture of CO2 was examined. CO2 breakthrough time and adsorption capacities were tested in the MVA system and compared to a vibrating fluidized bed (VFB) system. Experimental results showed that the improved fluidity in the MVA system enhanced CO2 adsorption capacity.
In order to aid future scaling up of the MVA process, the agglomerate size distribution in the MVA system was predicted by utilizing a force balance model coupled with a two-fluid model (TFM) simulation. The particle agglomerate size that was predicted using the computer simulation was validated with experimental data and found to be in good agreement.
Lastly, in order to demonstrate the utility of the MVA system in an air revitalization application, the capture of CO2 was examined. CO2 breakthrough time and adsorption capacities were tested in the MVA system and compared to a vibrating fluidized bed (VFB) system. Experimental results showed that the improved fluidity in the MVA system enhanced CO2 adsorption capacity.
Details
Title
- Fluidization of Nanosized Particles by a Microjet and Vibration Assisted (MVA) Method
Contributors
- An, Keju (Author)
- Andino, Jean (Thesis advisor)
- Phelan, Patrick (Thesis advisor)
- Adrian, Ronald (Committee member)
- Emady, Heather (Committee member)
- Kasbaoui, Mohamed (Committee member)
- Arizona State University (Publisher)
Date Created
The date the item was original created (prior to any relationship with the ASU Digital Repositories.)
2019
Subjects
Resource Type
Collections this item is in
Note
- Doctoral Dissertation Mechanical Engineering 2019