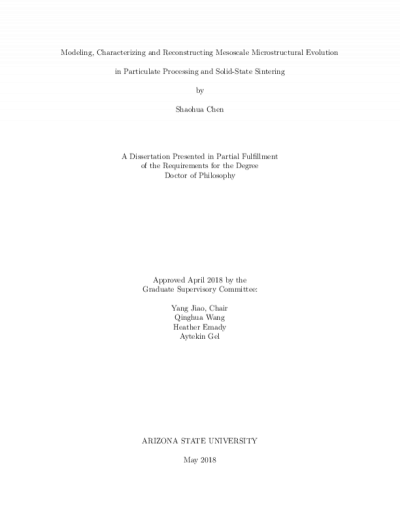
Description
In material science, microstructure plays a key role in determining properties, which further determine utility of the material. However, effectively measuring microstructure evolution in real time remains an challenge. To date, a wide range of advanced experimental techniques have been developed and applied to characterize material microstructure and structural evolution on different length and time scales. Most of these methods can only resolve 2D structural features within a narrow range of length scale and for a single or a series of snapshots. The currently available 3D microstructure characterization techniques are usually destructive and require slicing and polishing the samples each time a picture is taken. Simulation methods, on the other hand, are cheap, sample-free and versatile without the special necessity of taking care of the physical limitations, such as extreme temperature or pressure, which are prominent
issues for experimental methods. Yet the majority of simulation methods are limited to specific circumstances, for example, first principle computation can only handle several thousands of atoms, molecular dynamics can only efficiently simulate a few seconds of evolution of a system with several millions particles, and finite element method can only be used in continuous medium, etc. Such limitations make these individual methods far from satisfaction to simulate macroscopic processes that a material sample undergoes up to experimental level accuracy. Therefore, it is highly desirable to develop a framework that integrate different simulation schemes from various scales
to model complicated microstructure evolution and corresponding properties. Guided by such an objective, we have made our efforts towards incorporating a collection of simulation methods, including finite element method (FEM), cellular automata (CA), kinetic Monte Carlo (kMC), stochastic reconstruction method, Discrete Element Method (DEM), etc, to generate an integrated computational material engineering platform (ICMEP), which could enable us to effectively model microstructure evolution and use the simulated microstructure to do subsequent performance analysis. In this thesis, we will introduce some cases of building coupled modeling schemes and present
the preliminary results in solid-state sintering. For example, we use coupled DEM and kinetic Monte Carlo method to simulate solid state sintering, and use coupled FEM and cellular automata method to model microstrucutre evolution during selective laser sintering of titanium alloy. Current results indicate that joining models from different length and time scales is fruitful in terms of understanding and describing microstructure evolution of a macroscopic physical process from various perspectives.
issues for experimental methods. Yet the majority of simulation methods are limited to specific circumstances, for example, first principle computation can only handle several thousands of atoms, molecular dynamics can only efficiently simulate a few seconds of evolution of a system with several millions particles, and finite element method can only be used in continuous medium, etc. Such limitations make these individual methods far from satisfaction to simulate macroscopic processes that a material sample undergoes up to experimental level accuracy. Therefore, it is highly desirable to develop a framework that integrate different simulation schemes from various scales
to model complicated microstructure evolution and corresponding properties. Guided by such an objective, we have made our efforts towards incorporating a collection of simulation methods, including finite element method (FEM), cellular automata (CA), kinetic Monte Carlo (kMC), stochastic reconstruction method, Discrete Element Method (DEM), etc, to generate an integrated computational material engineering platform (ICMEP), which could enable us to effectively model microstructure evolution and use the simulated microstructure to do subsequent performance analysis. In this thesis, we will introduce some cases of building coupled modeling schemes and present
the preliminary results in solid-state sintering. For example, we use coupled DEM and kinetic Monte Carlo method to simulate solid state sintering, and use coupled FEM and cellular automata method to model microstrucutre evolution during selective laser sintering of titanium alloy. Current results indicate that joining models from different length and time scales is fruitful in terms of understanding and describing microstructure evolution of a macroscopic physical process from various perspectives.
Details
Title
- Modeling, characterizing and reconstructing mesoscale microstructural evolution in particulate processing and solid-state sintering
Contributors
- Chen, Shaohua (Author)
- Jiao, Yang (Thesis advisor)
- Wang, Qinghua (Committee member)
- Emady, Heather (Committee member)
- Gel, Aytekin (Committee member)
- Arizona State University (Publisher)
Date Created
The date the item was original created (prior to any relationship with the ASU Digital Repositories.)
2018
Subjects
Resource Type
Collections this item is in
Note
- thesisPartial requirement for: Ph.D., Arizona State University, 2018
- bibliographyIncludes bibliographical references (pages 125-142)
- Field of study: Materials science and engineering
Citation and reuse
Statement of Responsibility
by Shaohua Chen