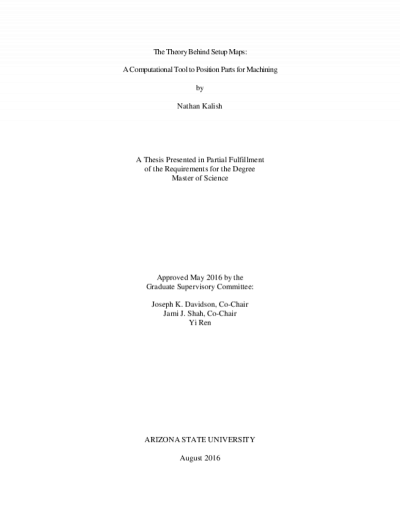
Description
When manufacturing large or complex parts, often a rough operation such as casting is used to create the majority of the part geometry. Due to the highly variable nature of the casting process, for mechanical components that require precision surfaces for functionality or assembly with others, some of the important features are machined to specification. Depending on the relative locations of as-cast to-be-machined features and the amount of material at each, the part may be positioned or ‘set up’ on a fixture in a configuration that will ensure that the pre-specified machining operations will successfully clean up the rough surfaces and produce a part that conforms to any assigned tolerances. For a particular part whose features incur excessive deviation in the casting process, it may be that no setup would yield an acceptable final part. The proposed Setup-Map (S-Map) describes the positions and orientations of a part that will allow for it to be successfully machined, and will be able to determine if a particular part cannot be made to specification.
The Setup Map is a point space in six dimensions where each of the six orthogonal coordinates corresponds to one of the rigid-body displacements in three dimensional space: three rotations and three translations. Any point within the boundaries of the Setup-Map (S-Map) corresponds to a small displacement of the part that satisfies the condition that each feature will lie within its associated tolerance zone after machining. The process for creating the S-Map involves the representation of constraints imposed by the tolerances in simple coordinate systems for each to-be-machined feature. Constraints are then transformed to a single coordinate system where the intersection reveals the common allowable ‘setup’ points. Should an intersection of the six-dimensional constraints exist, an optimization scheme is used to choose a single setup that gives the best chance for machining to be completed successfully. Should no intersection exist, the particular part cannot be machined to specification or must be re-worked with weld metal added to specific locations.
The Setup Map is a point space in six dimensions where each of the six orthogonal coordinates corresponds to one of the rigid-body displacements in three dimensional space: three rotations and three translations. Any point within the boundaries of the Setup-Map (S-Map) corresponds to a small displacement of the part that satisfies the condition that each feature will lie within its associated tolerance zone after machining. The process for creating the S-Map involves the representation of constraints imposed by the tolerances in simple coordinate systems for each to-be-machined feature. Constraints are then transformed to a single coordinate system where the intersection reveals the common allowable ‘setup’ points. Should an intersection of the six-dimensional constraints exist, an optimization scheme is used to choose a single setup that gives the best chance for machining to be completed successfully. Should no intersection exist, the particular part cannot be machined to specification or must be re-worked with weld metal added to specific locations.
Details
Title
- The theory behind setup maps: a computational tool to position parts for machining
Contributors
- Kalish, Nathan (Author)
- Davidson, Joseph K. (Thesis advisor)
- Shah, Jami J. (Thesis advisor)
- Ren, Yi (Committee member)
- Arizona State University (Publisher)
Date Created
The date the item was original created (prior to any relationship with the ASU Digital Repositories.)
2016
Subjects
Resource Type
Collections this item is in
Note
- thesisPartial requirement for: M.S., Arizona State University, 2016
- bibliographyIncludes bibliographical references (pages 88-89)
- Field of study: Engineering
Citation and reuse
Statement of Responsibility
by Nathan Kalish