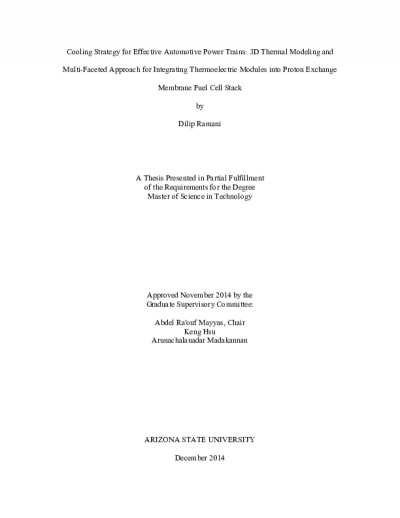
Description
Current hybrid vehicle and/or Fuel Cell Vehicle (FCV) use both FC and an electric system. The sequence of the electric power train with the FC system is intended to achieve both better fuel economies than the conventional vehicles and higher performance. Current hybrids use regenerative braking technology, which converts the vehicles kinetic energy into electric energy instead of wasting it. A hybrid vehicle is much more fuel efficient than conventional Internal Combustion (IC) engine and has less environmental impact The new hybrid vehicle technology with it's advanced with configurations (i.e. Mechanical intricacy, advanced driving modes etc) inflict an intrusion with the existing Thermal Management System (TMS) of the conventional vehicles. This leaves for the opportunity for now thermal management issues which needed to be addressed. Till date, there has not been complete literature on thermal management issued of FC vehicles. The primary focus of this dissertation is on providing better cooling strategy for the advanced power trains. One of the cooling strategies discussed here is the thermo-electric modules.
The 3D Thermal modeling of the FC stack utilizes a Finite Differencing heat approach method augmented with empirical boundary conditions is employed to develop 3D thermal model for the integration of thermoelectric modules with Proton Exchange Membrane fuel cell stack. Hardware-in-Loop was designed under pre-defined drive cycle to obtain fuel cell performance parameters along with anode and cathode gas flow-rates and surface temperatures. The FC model, combined experimental and finite differencing nodal net work simulation modeling approach which implemented heat generation across the stack to depict the chemical composition process. The structural and temporal temperature contours obtained from this model are in compliance with the actual recordings obtained from the infrared detector and thermocouples. The Thermography detectors were set-up through dual band thermography to neutralize the emissivity and to give several dynamic ranges to achieve accurate temperature measurements. The thermocouples network was installed to provide a reference signal.
The model is harmonized with thermo-electric modules with a modeling strategy, which enables optimize better temporal profile across the stack. This study presents the improvement of a 3D thermal model for proton exchange membrane fuel cell stack along with the interfaced thermo-electric module. The model provided a virtual environment using a model-based design approach to assist the design engineers to manipulate the design correction earlier in the process and eliminate the need for costly and time consuming prototypes.
The 3D Thermal modeling of the FC stack utilizes a Finite Differencing heat approach method augmented with empirical boundary conditions is employed to develop 3D thermal model for the integration of thermoelectric modules with Proton Exchange Membrane fuel cell stack. Hardware-in-Loop was designed under pre-defined drive cycle to obtain fuel cell performance parameters along with anode and cathode gas flow-rates and surface temperatures. The FC model, combined experimental and finite differencing nodal net work simulation modeling approach which implemented heat generation across the stack to depict the chemical composition process. The structural and temporal temperature contours obtained from this model are in compliance with the actual recordings obtained from the infrared detector and thermocouples. The Thermography detectors were set-up through dual band thermography to neutralize the emissivity and to give several dynamic ranges to achieve accurate temperature measurements. The thermocouples network was installed to provide a reference signal.
The model is harmonized with thermo-electric modules with a modeling strategy, which enables optimize better temporal profile across the stack. This study presents the improvement of a 3D thermal model for proton exchange membrane fuel cell stack along with the interfaced thermo-electric module. The model provided a virtual environment using a model-based design approach to assist the design engineers to manipulate the design correction earlier in the process and eliminate the need for costly and time consuming prototypes.
Details
Title
- Cooling strategy for effective automotive power trains: 3D thermal modeling and multi-faceted approach for integrating thermoelectric modules into proton exchange membrane fuel cell stack
Contributors
- Ramani, Dilip (Author)
- Mayyas, Abdel Ra'Ouf (Thesis advisor)
- Hsu, Keng (Committee member)
- Madakannan, Arunachalanadar (Committee member)
- Arizona State University (Publisher)
Date Created
The date the item was original created (prior to any relationship with the ASU Digital Repositories.)
2014
Subjects
Resource Type
Collections this item is in
Note
- thesisPartial requirement for: M.S., Arizona State University, 2014
- bibliographyIncludes bibliographical references (p. 54-59)
- Field of study: Technology
Citation and reuse
Statement of Responsibility
by Dilip Ramani