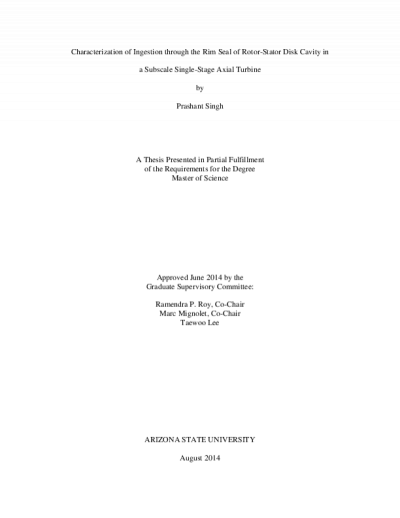
Description
In order to achieve higher gas turbine efficiency, the main gas temperature at turbine inlet has been steadily increased from approximately 900°C to about 1500°C over the last few decades. This temperature is higher than the maximum acceptable temperature for turbine internals. The hot main gas may get ingested into the space between rotor and stator, the rotor-stator disk cavity in a stage because of the pressure differential between main gas annulus and the disk cavity. To reduce this ingestion, the disk cavity is equipped with a rim seal; additionally, secondary (purge) air is supplied to the cavity. Since the purge air is typically bled off the compressor discharge, this reducing the overall gas turbine efficiency, much research has been carried out to estimate the minimum purge flow necessary (cw,min) for complete sealing of disk cavities.
In this work, experiments have been performed in a subscale single-stage axial turbine featuring vanes, blades and an axially-overlapping radial-clearance seal at the disk cavity rim. The turbine stage is also equipped with a labyrinth seal radially inboard. The stage geometry and the experimental conditions were such that the ingestion into the disk cavity was driven by the pressure asymmetry in the main gas annulus. In the experiments, time-averaged static pressure was measured at several locations in the main annulus and in the disk cavity; the pressure differential between a location on the vane platform close to lip (this being the rim seal part on the stator) and a location in the 'seal region' in the cavity is considered to be the driving potential for both ingestion and egress. Time-averaged volumetric concentration of the tracer gas (CO2) in the purge air supplied was measured at multiple radial locations on the stator surface. The pressure and ingestion data were then used to calculate the ingestion and egress discharge coefficients for a range of purge flow rates, employing a simple orifice model of the rim seal. For the experiments performed, the egress discharge coefficient increased and the ingestion discharge coefficient decreased with the purge air flow rate. A method for estimation of cw,min is also proposed.
In this work, experiments have been performed in a subscale single-stage axial turbine featuring vanes, blades and an axially-overlapping radial-clearance seal at the disk cavity rim. The turbine stage is also equipped with a labyrinth seal radially inboard. The stage geometry and the experimental conditions were such that the ingestion into the disk cavity was driven by the pressure asymmetry in the main gas annulus. In the experiments, time-averaged static pressure was measured at several locations in the main annulus and in the disk cavity; the pressure differential between a location on the vane platform close to lip (this being the rim seal part on the stator) and a location in the 'seal region' in the cavity is considered to be the driving potential for both ingestion and egress. Time-averaged volumetric concentration of the tracer gas (CO2) in the purge air supplied was measured at multiple radial locations on the stator surface. The pressure and ingestion data were then used to calculate the ingestion and egress discharge coefficients for a range of purge flow rates, employing a simple orifice model of the rim seal. For the experiments performed, the egress discharge coefficient increased and the ingestion discharge coefficient decreased with the purge air flow rate. A method for estimation of cw,min is also proposed.
Details
Title
- Characterization of ingestion through the rim seal of rotor-stator disk cavity in a subscale single-stage axial turbine
Contributors
- Singh, Prashant (Author)
- Roy, Ramendra P (Thesis advisor)
- Mignolet, Marc (Thesis advisor)
- Lee, Taewoo (Committee member)
- Arizona State University (Publisher)
Date Created
The date the item was original created (prior to any relationship with the ASU Digital Repositories.)
2014
Resource Type
Collections this item is in
Note
- thesisPartial requirement for: M.S., Arizona State University, 2014
- bibliographyIncludes bibliographical references (p. 72-75)
- Field of study: Mechanical engineering
Citation and reuse
Statement of Responsibility
by Prashant Singh