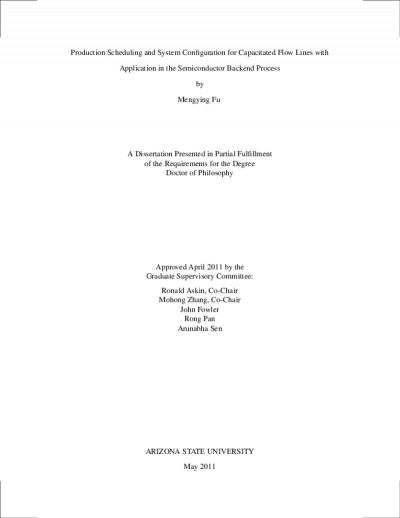
Description
A good production schedule in a semiconductor back-end facility is critical for the on time delivery of customer orders. Compared to the front-end process that is dominated by re-entrant product flows, the back-end process is linear and therefore more suitable for scheduling. However, the production scheduling of the back-end process is still very difficult due to the wide product mix, large number of parallel machines, product family related setups, machine-product qualification, and weekly demand consisting of thousands of lots. In this research, a novel mixed-integer-linear-programming (MILP) model is proposed for the batch production scheduling of a semiconductor back-end facility. In the MILP formulation, the manufacturing process is modeled as a flexible flow line with bottleneck stages, unrelated parallel machines, product family related sequence-independent setups, and product-machine qualification considerations. However, this MILP formulation is difficult to solve for real size problem instances. In a semiconductor back-end facility, production scheduling usually needs to be done every day while considering updated demand forecast for a medium term planning horizon. Due to the limitation on the solvable size of the MILP model, a deterministic scheduling system (DSS), consisting of an optimizer and a scheduler, is proposed to provide sub-optimal solutions in a short time for real size problem instances. The optimizer generates a tentative production plan. Then the scheduler sequences each lot on each individual machine according to the tentative production plan and scheduling rules. Customized factory rules and additional resource constraints are included in the DSS, such as preventive maintenance schedule, setup crew availability, and carrier limitations. Small problem instances are randomly generated to compare the performances of the MILP model and the deterministic scheduling system. Then experimental design is applied to understand the behavior of the DSS and identify the best configuration of the DSS under different demand scenarios. Product-machine qualification decisions have long-term and significant impact on production scheduling. A robust product-machine qualification matrix is critical for meeting demand when demand quantity or mix varies. In the second part of this research, a stochastic mixed integer programming model is proposed to balance the tradeoff between current machine qualification costs and future backorder costs with uncertain demand. The L-shaped method and acceleration techniques are proposed to solve the stochastic model. Computational results are provided to compare the performance of different solution methods.
Details
Title
- Production scheduling and system configuration for capacitated flow lines with application in the semiconductor backend process
Contributors
- Fu, Mengying (Author)
- Askin, Ronald G. (Thesis advisor)
- Zhang, Muhong (Thesis advisor)
- Fowler, John W (Committee member)
- Pan, Rong (Committee member)
- Sen, Arunabha (Committee member)
- Arizona State University (Publisher)
Date Created
The date the item was original created (prior to any relationship with the ASU Digital Repositories.)
2011
Subjects
- Industrial Engineering
- Operations Research
- Flexible Flow Shop
- heuristic
- Optimization
- Scheduling
- Semiconductor Back-end Process
- Stochastic programming
- Production scheduling
- Stochastic Models
- Semiconductor industry--Linear programming.
- Semiconductor Industry
- Manufacturing processes--Planning.
- Manufacturing processes
Resource Type
Collections this item is in
Note
- thesisPartial requirement for: Ph.D., Arizona State University, 2011
- Includes bibliographical references (p
- Field of study: Industrial engineering
Citation and reuse
Statement of Responsibility
Mengying Fu