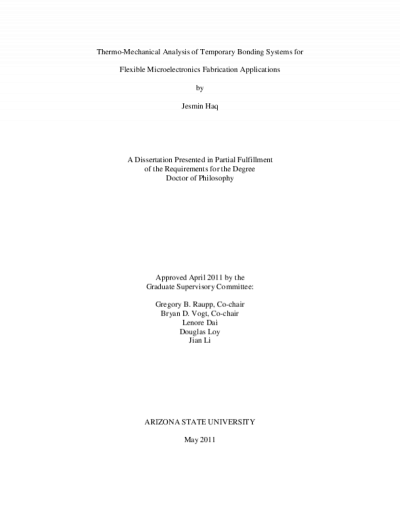
Description
Temporary bonding-debonding of flexible plastic substrates to rigid carriers may facilitate effective substrate handling by automated tools for manufacture of flexible microelectronics. The primary challenges in implementing practical temporary bond-debond technology originate from the stress that is developed during high temperature processing predominately through thermal-mechanical property mismatches between carrier, adhesive and substrate. These stresses are relaxed through bowing of the bonded system (substrate-adhesive-carrier), which causes wafer handling problems, or through delamination of substrate from rigid carrier. Another challenge inherent to flexible plastic substrates and linked to stress is their dimensional instability, which may manifest itself in irreversible deformation upon heating and cooling cycles. Dimensional stability is critical to ensure precise registration of different layers during photolithography. The global objective of this work is to determine comprehensive experimental characterization and develop underlying fundamental engineering concept that could enable widespread adoption and scale-up of temporary bonding processing protocols for flexible microelectronics manufacturing. A series of carriers with different coefficient of thermal expansion (CTE), modulus and thickness were investigated to correlate the thermo-mechanical properties of carrier with deformation behavior of bonded systems. The observed magnitude of system bow scaled with properties of carriers according to well-established Stoney's equation. In addition, rheology of adhesive impacted the deformation of bonded system. In particular, distortion-bowing behavior correlated directly with the relative loss factor of adhesive and flexible plastic substrate. Higher loss factor of adhesive compared to that of substrate allowed the stress to be relaxed with less bow, but led to significantly greater dimensional distortion. Conversely, lower loss factor of adhesive allowed less distortion but led to larger wafer bow. A finite element model using ANSYS was developed to predict the trend in bow-distortion of bonded systems as a function of the viscoelastic properties of adhesive. Inclusion of the viscoelasticity of flexible plastic substrate itself was critical to achieving good agreement between simulation and experiment. Simulation results showed that there is a limited range within which tuning the rheology of adhesive can control the stress-distortion. Therefore, this model can aid in design of new adhesive formulations compatible with different processing requirements of various flexible microelectronics applications.
Details
Title
- Thermo-mechanical analysis of temporary bonding systems for flexible microelectronics fabrication applications
Contributors
- Haq, Jesmin (Author)
- Raupp, Gregory B (Thesis advisor)
- Vogt, Bryan D (Thesis advisor)
- Dai, Lenore (Committee member)
- Loy, Douglas (Committee member)
- Li, Jian (Committee member)
- Arizona State University (Publisher)
Date Created
The date the item was original created (prior to any relationship with the ASU Digital Repositories.)
2011
Subjects
Resource Type
Collections this item is in
Note
- thesisPartial requirement for: Ph.D., Arizona State University, 2011
- bibliographyIncludes bibliographical references
- Field of study: Chemical engineering
Citation and reuse
Statement of Responsibility
Jesmin Haq