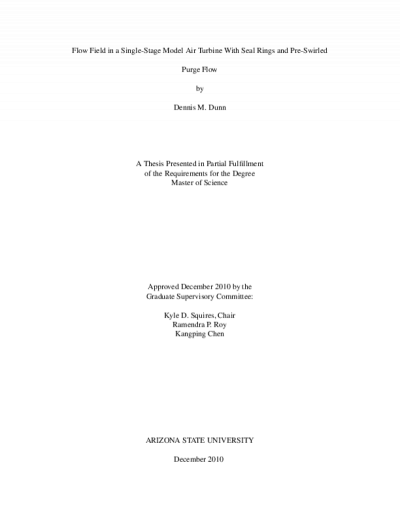
Description
Modern gas turbines operate at high mainstream gas temperatures and pressures, which requires high durability materials. A method of preventing these hot gases from leaking into the turbine cavities is essential for improved reliability and cost reduction. Utilizing bleed-off air from the compressor to cool internal components has been a common solution, but at the cost of decreasing turbine performance. The present work thoroughly describes the complex flow field between the mainstream gas and a single rotor-stator disk cavity, and mechanisms of mainstream gas ingestion. A combined approach of experimental measurement and numerical simulation are performed on the flow in a single-stage model gas turbine. Mainstream gas ingestion into the cavity is further reduced by utilizing two axially overlapping seal rings, one on the rotor disk and the other on the stator wall. Secondary purge air is injected into the rotor-stator cavity pre-swirled through the stator radially inboard of the two seal rings. Flow field predictions from the simulations are compared against experimental measurements of static pressure, velocity, and tracer gas concentration acquired in a nearly identical model configuration. Operational conditions were performed with a main airflow Reynolds number of 7.86e4 and a rotor disk speed of 3000rpm. Additionally the rotational Reynolds number was 8.74e5 with a purge air nondimensional flow rate cw=4806. The simulation models a 1/14 rotationally periodic sector of the turbine rig, consisting of four rotor blades and four stator vanes. Gambit was used to generate the three-dimensional unstructured grids ranging from 10 to 20 million cells. Effects of turbulence were modeled using the single-equation Spalart-Allmaras as well as the realizable k-epsilon models. Computations were performed using FLUENT for both a simplified steady-state and subsequent time-dependent formulation. Simulation results show larger scale structures across the entire sector angle inside the cavity and certain unsteady mainstream ingestion mechanisms are realized from the tracer gas. Simulated velocity distributions were scrutinized against Particle Image Velocimetry plots in the rotor-stator cavity and are in reasonable agreement with all of the measurements.
Details
Title
- Flow field in a single-stage model air turbine with seal rings and pre-swirled purge flow
Contributors
- Dunn, Dennis Martin (Author)
- Squires, Kyle D (Thesis advisor)
- Roy, Ramendra P (Committee member)
- Chen, Kangping (Committee member)
- Arizona State University (Publisher)
Date Created
The date the item was original created (prior to any relationship with the ASU Digital Repositories.)
2010
Subjects
Resource Type
Collections this item is in
Note
- thesisPartial requirement for: M.S., Arizona State University, 2010
- bibliographyIncludes bibliographical references (p. 99-101)
- Field of study: Mechanical engineering
Citation and reuse
Statement of Responsibility
Dennis Martin Dunn