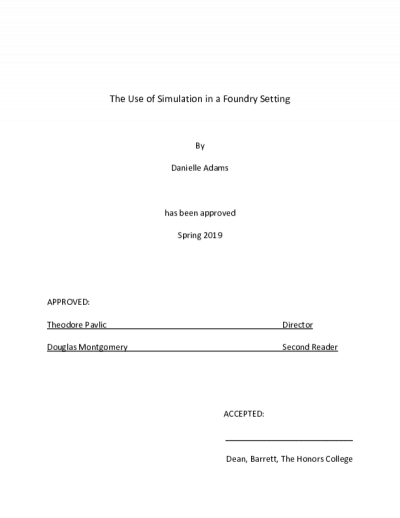
Description
Woodland/Alloy Casting, Inc. is an aluminum foundry known for providing high-quality molds to their customers in industries such as aviation, electrical, defense, and nuclear power. However, as the company has grown larger during the past three years, they have begun to struggle with the on-time delivery of their orders. Woodland prides itself on their high-grade process that includes core processing, the molding process, cleaning process, and heat-treat process. To create each mold, it has to flow through each part of the system flawlessly. Throughout this process, significant bottlenecks occur that limit the number of molds leaving the system. To combat this issue, this project uses a simulation of the foundry to test how best to schedule their work to optimize the use of their resources. Simulation can be an effective tool when testing for improvements in systems where making changes to the physical system is too expensive. ARENA is a simulation tool that allows for manipulation of resources and process while also allowing both random and selected schedules to be run through the foundry’s production process. By using an ARENA simulation to test different scheduling techniques, the risk of missing production runs is minimized during the experimental period so that many different options can be tested to see how they will affect the production line. In this project, several feasible scheduling techniques are compared in simulation to determine which schedules allow for the highest number of molds to be completed.
Details
Title
- The Use of Simulation in a Foundry Setting
Contributors
- Adams, Danielle Renee (Author)
- Pavlic, Theodore (Thesis director)
- Montgomery, Douglas (Committee member)
- Industrial, Systems & Operations Engineering Prgm (Contributor)
- Barrett, The Honors College (Contributor)
Date Created
The date the item was original created (prior to any relationship with the ASU Digital Repositories.)
2019-05
Subjects
Resource Type
Collections this item is in